Central Texas Solar Project
- Application:
- Stabilization
- Products Used:
- Flexamat
- Location:
- Central
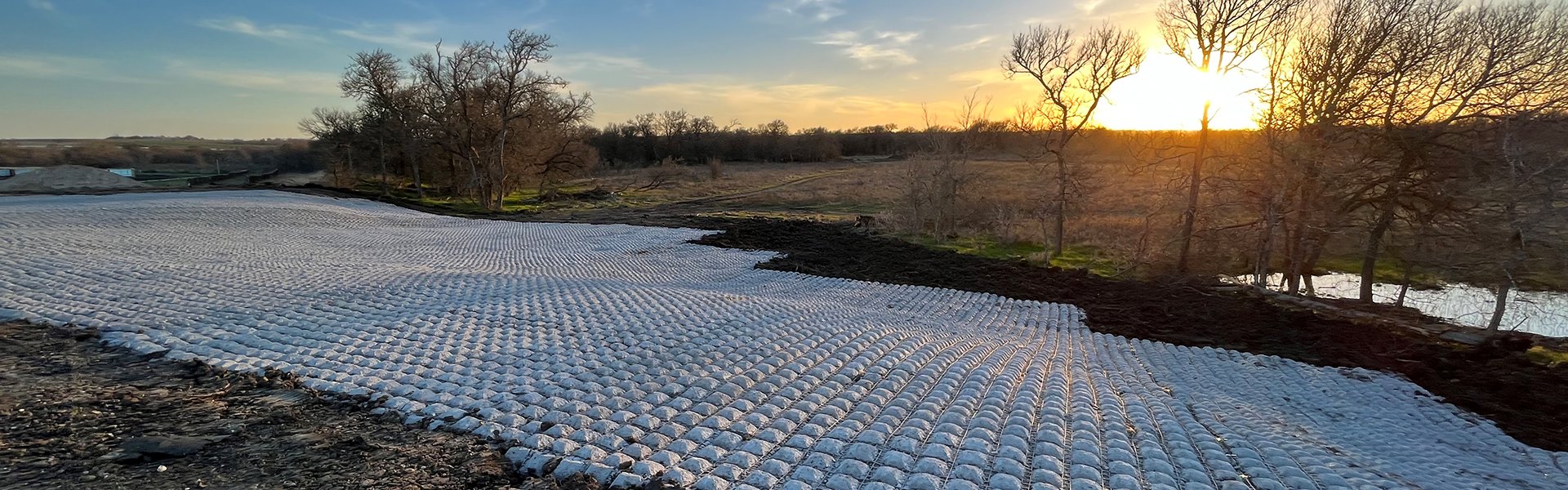
Notes
This case study showcases the advantages of using Flexamat concrete block matting as an alternative to riprap for low water crossings and adjacent slopes on a solar farm in Central Texas. The project’s goals were to mitigate erosion through stabilization and reinforcement, while minimizing environmental impact, speeding up construction and reducing costs. This project had several areas of concern from an erosion perspective, and generally speaking, low water crossings are prone to significant erosion due to the combination of truck traffic and the potential of heavy rainfall creating high-velocity flows. Riprap was not ideal because of its costly and time-consuming installation and the long haul from the quarry.
Flexamat was chosen as the alternative to riprap for both the low water crossing and adjacent slopes. The product consists of 5000 psi concrete blocks cast onto/through a high-strength biaxial geogrid. For the sloped areas, vegetation establishment through the matting was expected, so turf reinforcement mats and excelsior fibers were used as backing. For the low water crossings, vegetation was not anticipated, so a non-woven geotextile backing was utilized in these areas. The subgrade was prepared by removing debris and leveling the surface. For the low water crossings, several inches of aggregate was installed and compacted to stabilize the subgrade. Flexamat was then unrolled over the prepared surface, anchor-trenched appropriately, and stainless-steel zip ties were utilized to secure the overlaps. For the low water crossings, crushed aggregate was then used to infill between the concrete blocks to provide a smoother driving surface, and the sloped areas were seeded in order to get vegetation establishment.
The use of Flexamat proved to be a successful and sustainable solution. It provides long-term stability and resistance to shear stress. Compared to traditional riprap solutions, it has minimal environmental impact (reduction of trucking), faster installation time, and typically lower overall costs. This demonstrates Flexamat’s potential as a viable alternative to traditional riprap solutions for similar projects.